Sandwich Pavilion: Timber Connection, Architectural Form and Building Method Discovery
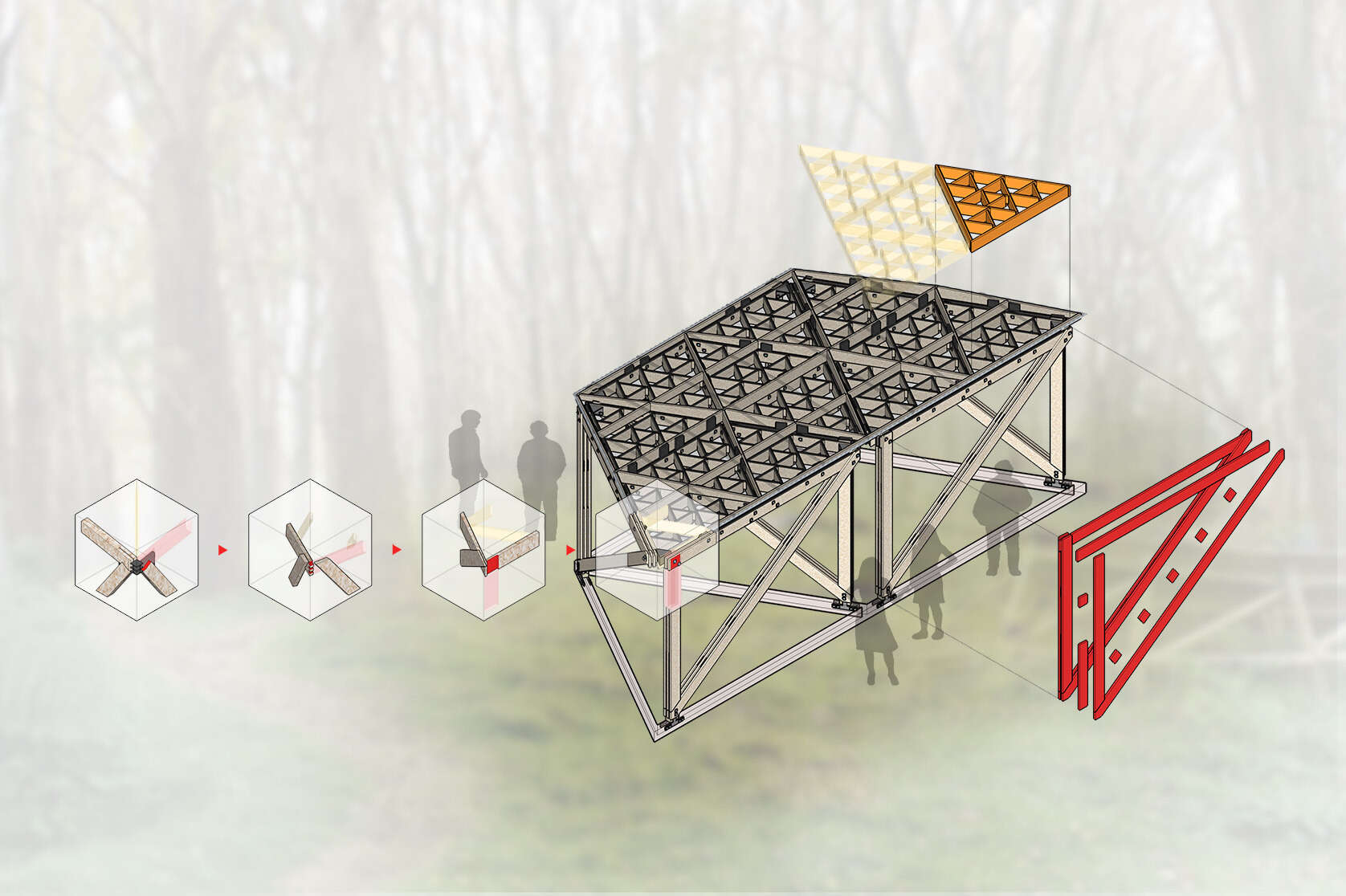
In this thesis, the whole building process goes back to a simple, classic working environment, with a basic machine supply. It also tries to find a “sandwich” way to build a “complex” building with a simplified strategy in the whole building process.
The “sandwich” system provides not only beauty in the architectural and structural logic with all components working with the same timber profile dimension, but also different layers of overlapping to bear different loads from the primary to the tertiary level of structure.